Non Combustible Aluminium Composite Panels
ACROSS THE WORLD, ALUCOBOND® A2 is the only non-combustible aluminum composite panel used in architecture.
Due to its non-combustible core, this fantastic product meets stringent fire regulations and hugely increases the possibilities when it comes to creative building design.
As with all ALUCOBOND® products, ALUCOBOND® A2 allows for simple processing, is impact-resistant, break-proof, and weatherproof – and above all non-combustible.
Riveting is possible using solid or blind rivets with conventional riveting tools. For exterior applications allow for thermal expansion and use a rivet attachment jig if necessary. ALUCOBOND® A2 panels can be fastened together or joined to other materials using rivets commonly used in aluminium construction. For outdoor use and for use in areas of high humidity, make sure to use aluminium blind rivets with stainless steel mandrels to prevent unpleasant corrosive edges. When using aluminium blind rivets with steel mandrels, the mandrel should drop out after riveting (detachable version). Countersunk rivets are suitable for indoor use only.
For outdoor use please note:
- Use aluminium blind rivets that have been approved for construction with a 5mm shaft diameter and an attachment head diameter of 11mm or 14mm.
- Take the thermal expansion of the panel into account (2.4mm/m/100°C). To avoid jamming, the hole in the panel must be large enough to allow for expansion.
- With the shaft of the rivet fitting closely to the edge of the hole, the attachment head must cover 1mm of the area surrounding the hole.
- Multi-step drills or sleeves having corresponding diameters are used for centrically drilling holes into the panel and the substructure for centrically fitting the rivet.
- Rivet attachment jigs are used for fitting blind rivets without jamming, allowing for a tolerance of 0.3mm.
- Make sure to use rivet attachment jigs and rivets from the same manufacturer, as the height of the attachment head according to DIN 7337 may vary.
- The clamping thickness results from the thickness of the material to be riveted plus an additional value of 2mm to ensure that the closing head is perfectly formed. In accordance with this clamping thickness, the corresponding shaft length is determined in the tables provided by the rivet manufacturers. (Lmin = 14mm).
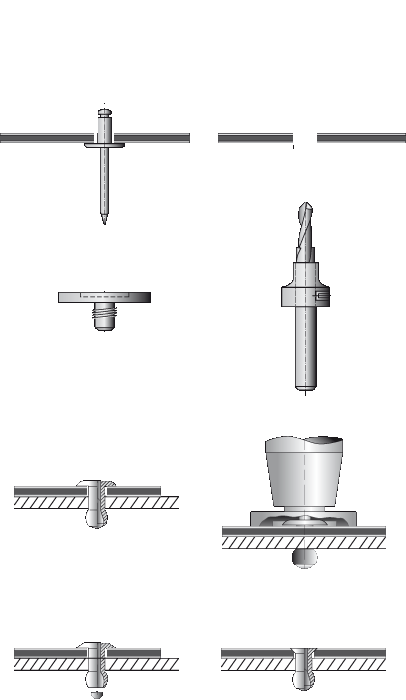